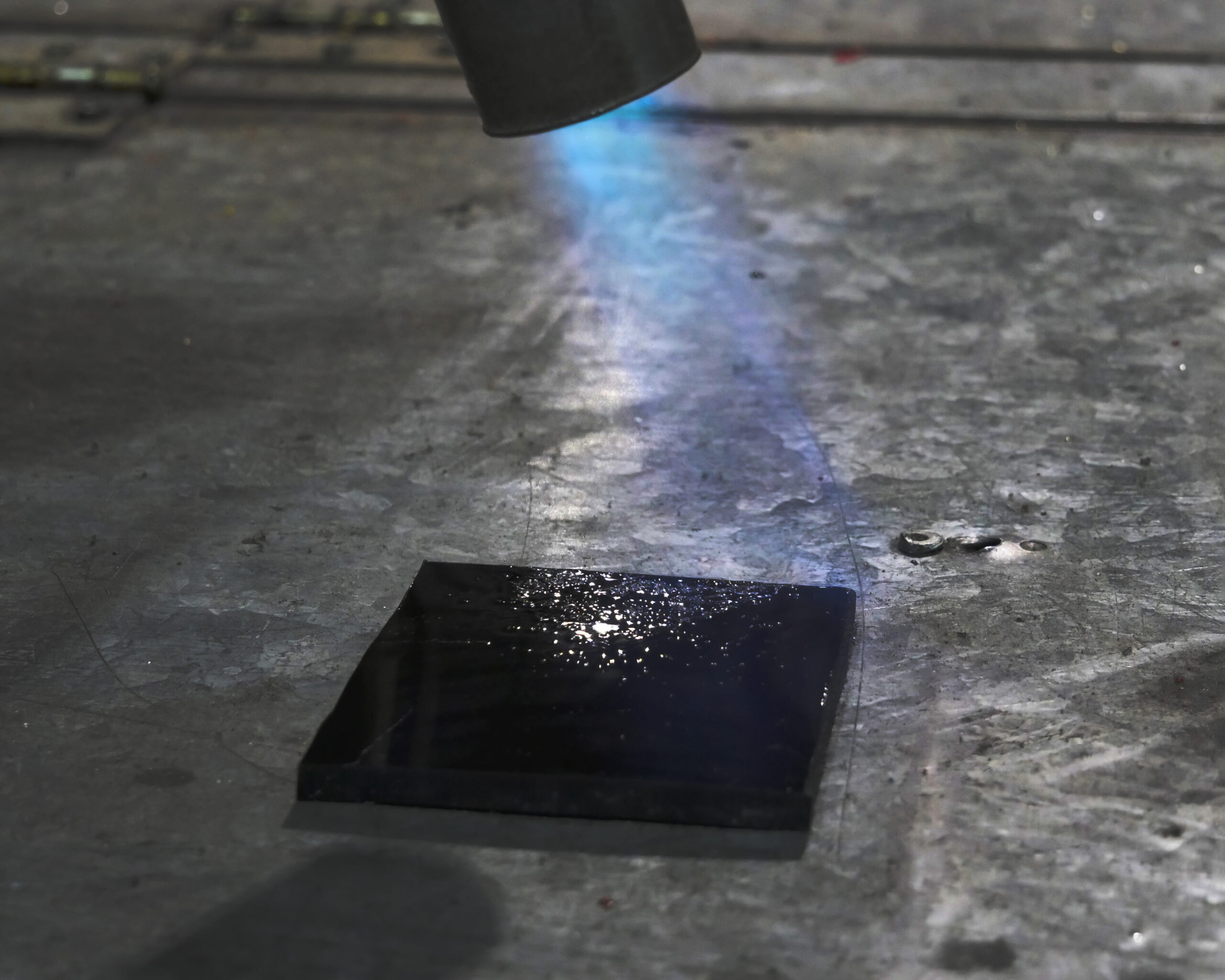
Urethanes are desired across a wide breadth of industries from food processing to aerospace for their superior physical strength and flexibility. While we’ve written plenty about the properties that make urethanes the material of choice in high-stress applications, you may be surprised to learn that urethanes can also perform well in high-heat environments. At PSI Urethanes we offer flame retardant urethanes, which are specially formulated to adhere to the highest standard in polymer flame resistance: UL 94V-0.
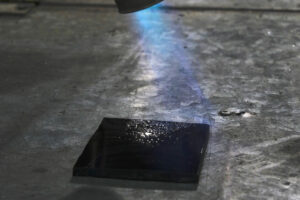
What Defines a Flame Retardant Urethane?
As the name suggests, a flame retardant or nonflammable urethane is able to prevent the spread of fire when exposed to a flame. In industries where high heat and fire are very real safety concerns, a self-extinguishing material like a nonflammable urethane can make a world of difference in facilitating a safer work environment.
While formulation is key to developing a flame-retardant urethane, what really defines a material as nonflammable is its performance in a controlled burn test. The most stringent burn test for urethane and other polymers is the UL 94V-0 test, in which a vertical test strip of material is exposed to a direct flame in two ten-second intervals. Whatever material melts off from the strip will fall onto a bed of flammable cotton below. In order to pass the test, the material drippings must not cause the cotton to burn.
At PSI, our thermoset urethanes can be formulated to meet any flame resistance standard up to UL 94V-0. With our high caliber of formulation capabilities, we develop urethanes for use in high-heat applications including automotive, aerospace, military, metalforming, and more.
Nonflammable Urethanes in Automotive, Aviation, and Aerospace
When it comes to high-temperature applications that could employ urethane parts, there is none more prevalent than locomotion. Automotive, aviation, and aerospace industries can all benefit from the use of nonflammable urethane parts.
High operating temperatures, finicky electrical components, and subsequent fire hazards are a given in both combustion engines and EVs alike. In the automotive industry, any precaution that can be taken to mitigate the risk of fire or explosion is worth investing in to protect the wellbeing of manufacturing personnel, drivers, and passengers everywhere. The same can be said for the aviation industry, which carries an exponentially higher risk of potential damage and injury caused by any fire-related incident. Lastly, the aerospace sector wouldn’t even be where it’s at today without the development of materials that possess outstanding temperature and flame resistance that’s required for vessels to leave and enter earth’s atmosphere.
While safety should always be a primary concern, another factor to consider is the performance of flame resistant urethanes in high heat environments. Rubber and plastic components are prone to permanent deformation and loss of elasticity when exposed to high temperatures, which makes them a poor choice for high heat applications. Plastics are especially dangerous due to the toxic gases they release upon burning. More expensive metal parts are not without their drawbacks either when you consider how metals can expand when exposed to heat, leading to slow deformation given enough time and exposure. For high-precision, high-heat applications, flame resistant urethanes are the clear material choice for performance that you can count on.
Polyurethane components are becoming more common in consumer vehicles by the day. Tubing, rings, gaskets, and motor mounts are just a few of the nonflammable urethane parts that we’ve seen used in the automotive industry for their improved safety in both engine and electrical components. Some manufacturers are even integrating polyurethane into vehicle interior trim pieces, like dashboards, to create a longer lasting part that improves cabin safety.
If you’re looking for a nonflammable elastomer solution, look no further than PSI Urethanes.
Contact us today to learn more!
Contact Us
How OEMs Use Nonflammable Urethanes
Many times, OEMs seek cast polyurethane parts from PSI Urethanes to use in their product assemblies. In some cases, the parts and assemblies that they produce are going to customers in other industries that could benefit from flame retardant components: automotive, electrical, and robotics just to name a few. Even if the manufacturer doesn’t know exactly what the part will be used for there will be guidelines and specifications that they are instructed to adhere to, and that definitely includes meeting strict flammability standards from time to time.
We work with all kinds of OEMs, many of which carry ISO certifications. In these cases, we provide cast urethane parts that are best suited to meet or exceed their industry’s flammability standards.
Robotics and Process Automation Applications for Flame Retardant Urethanes
Some of the more recent industries we’ve started collaborating with include process automation and robotics.
In the robotics industry, plastic components are sometimes not a viable material choice due to their poor resistance to high temperature and flames. If an issue with electronic or mechanical components were to cause any part of a robot to catch fire, those burning plastic components would create a major air quality hazard to any personnel in the vicinity. By using nonflammable urethane components in place of plastics, the potential safety hazards of robotics are drastically reduced.
Some robotic parts that can be upgraded to a nonflammable urethane material include grippers, internal parts, rollers, and wheels. Flame resistant urethanes can even be bonded to metal cores for superior durability in wheels and rollers.
We’re ready to start developing your nonflammable urethane part today!
Get started by contacting us today.
Contact Us
About PSI Urethanes
Since 1966, through our own independent research and activity in the Polyurethane Manufacturers Association, PSI Urethanes has stayed on the leading edge of urethane technology – including developing advances in new materials, comprehensive designs, and processing technologies. Today we are among the most respected and trusted suppliers of custom polyurethane products.
We operate from our 45,000-square-foot manufacturing facility in Austin, Texas, which houses an extensive stock of polyurethane products. Our fully equipped manufacturing facility includes a versatile range of processing machinery, which allows us to work on unique, one-of-a-kind projects, as well as high volume components. Our in-house engineering, tooling, and custom mold shop, produces custom and stock production orders with exceptionally fast turn-around times. From conception to prototyping, to final production runs, our technical representatives and design engineers will work closely with your staff to meet your critical tolerances and specifications. You are guaranteed to receive experienced, professional, and personalized service from the first contact through your on-time delivery, with complete confidentiality and dedication to protecting your good name.