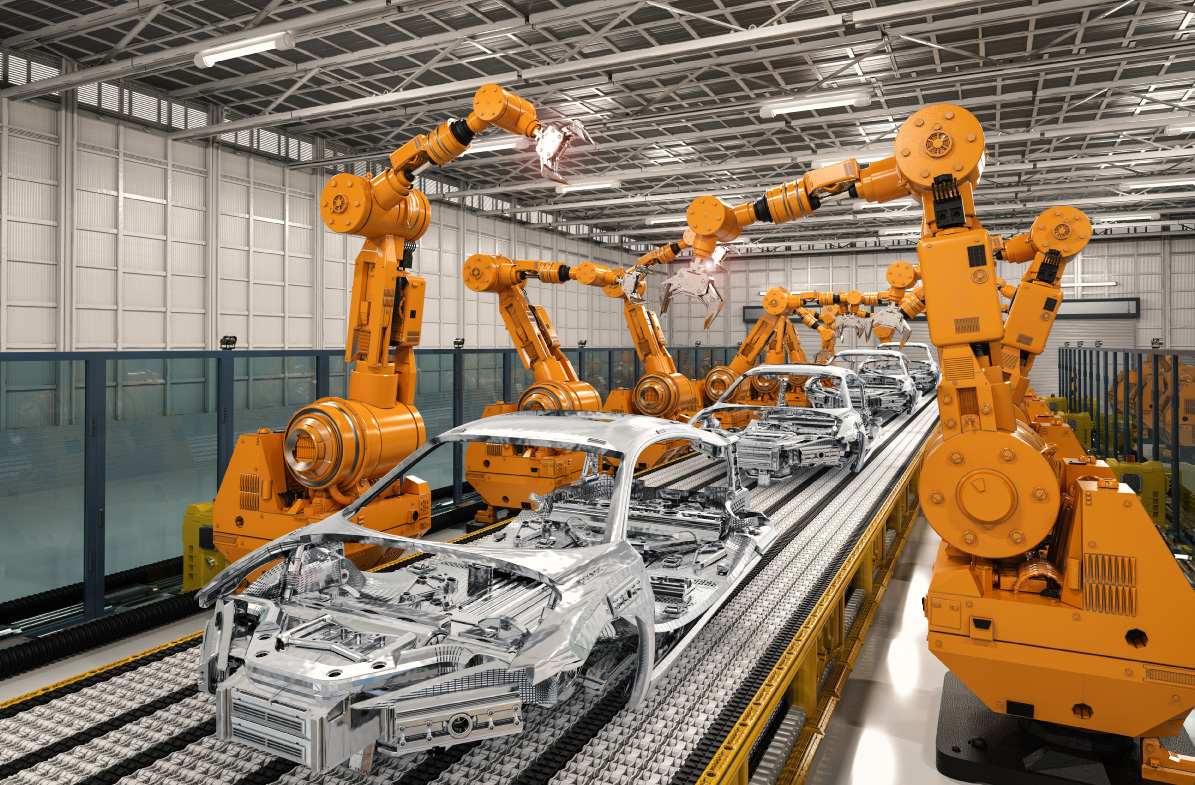
Advantages of Urethanes Over Other Elastomers
OEMs rely on urethanes to outperform and outlast the competition. Other commonly used elastomers, like rubber and other plastics, often fail even when subjected to anticipated regular wear and tear. While metal parts can offer a higher strength than those materials, making that switch eliminates the flexibility, light weight, and cost-effectiveness that comes with the use of an elastomer. When designing high quality parts, OEMs select urethane as their preferred material for its superior quality, longevity, and durability.
OEM parts are subjected to every type of wear that you can think of: impacts, high and low temperatures, abrasive chemicals, UV rays, tears, stretching, and more. Where other elastomers fail when exposed to these factors, urethane’s unparalleled mechanical and chemical resistance make it the clear choice for a product that’s meant to last.
Urethane’s durability can be largely attributed to its high resistance to mechanical damage. When compared to other elastomers, none even come close to displaying the same strength of urethane. In high impact applications, urethane’s shock absorption significantly reduces wear. In the opposite manner, it can also be stretched with a great resistance to tearing then easily bounce back to its original shape. Other physical factors like temperature, weather, and daily UV exposure have little effect on urethanes, whereas other elastomers are subject to dry out and rot.
Along with excellent mechanical properties, urethanes offer great sound and vibration dampening. This makes them a great replacement for not just elastomer parts, but also metal parts where noise and vibration can be a significant issue. Unlike metals, urethanes also demonstrate high levels of shock absorption when exposed to impact which reduces damage to both the urethane part and anything underneath. Its shock absorbing properties make urethane the preferred material for bushings, washers, bumpers, gaskets, and more.
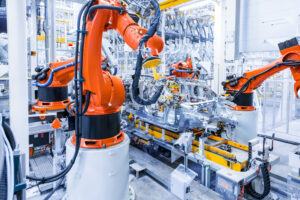
OEM Part Production at PSI Urethanes
From Sketch to Sample
Whatever stage of development your product may be in, PSI Urethanes has what it takes to bring your design into reality. If you’re still in the early design stages, we can help. Our experienced urethane engineers commonly work alongside customers who bring us a model, a design, or even a simple sketch. We can optimize your product design for ease of manufacturing without sacrificing function, effectively reducing costs for your project in the long run.
We can help you develop your OEM product.
Contact PSI Urethanes today for a consultation.
Contact Us
Urethane Prototypes and Production Runs for OEMs
Whether an OEM is seeking to produce just a few parts or a full-scale production run, PSI Urethanes has the flexibility to handle any order volume.
Thanks to the flexibility of our production system, we can produce a low volume of just a few pieces for prototyping purposes. This allows OEMs to get an idea of what adjustments need to be made to their part before moving on to production of the final product. Our engineering design team can help with this process to ensure the smoothest production run possible.
Our facility is fully equipped with mills, lathes, and other CNC machines to produce high-quality rapid prototypes for OEMs. Our variety of forming tools allow us to carefully shape all defined features of a prototype to your specifications. Once the design has been finalized, we can proceed with a full-scale production run of your part.
While our machine shop allows us to produce low volume runs for prototyping and other needs, it also has the capacity to handle high-volume orders. Our machines give PSI Urethanes the unique ability to produce product molds for cast urethane products in house, which speeds up high volume production and reduces the overall cost per part.
Custom Formulations for OEMs
PSI’s ability to formulate custom urethanes comes in especially handy for parts used by OEMs. We can modify any of the features of our urethanes from hardness to tear resistance to even cosmetic choices like color.
Parts used in OEM applications typically need higher levels of durability, chemical resistance, and heat resistance. These can all be achieved through the development of custom urethane formulations. When it comes to heat resistance, PSI Urethanes is even capable of providing custom parts that meet standards as stringent as UL 94V-0, a classification given only to the most flame-resistant materials. This, combined with a high chemical resistance, makes urethane an excellent material to be used in applications where an OEM part will be exposed to oils, lubricants, liquid fuels, and high heat.
In some rare cases an OEM might need a part that features the flexibility and strength of urethane alongside a level of electric conductivity. For these cases we present static dissipative urethanes, which offer a degree of electron movement throughout the part thanks to the addition of conductive carbon nanotubes.
Urethanes exhibit a wide range of desirable properties that make them a suitable choice to replace plastic, rubber, and metal parts alike. No other material offers the same level of high quality and customization to suit such a wide range of applications. These features combined with a quick and cost-effective method of production is why OEMs choose urethanes.
Our unique production capabilities combined with our outstanding finished quality are why OEMs choose PSI Urethanes.
Contact us today to learn more!
Contact Us
About PSI Urethanes
Since 1966, through our own independent research and activity in the Polyurethane Manufacturers Association, PSI Urethanes has stayed on the leading edge of urethane technology – including developing advances in new materials, comprehensive designs, and processing technologies. Today we are among the most respected and trusted suppliers of custom polyurethane products.
We operate from our 45,000-square-foot manufacturing facility in Austin, Texas, which houses an extensive stock of polyurethane products. Our fully equipped manufacturing facility includes a versatile range of processing machinery, which allows us to work on unique, one-of-a-kind projects, as well as high volume components. Our in-house engineering, tooling, and custom mold shop, produces custom and stock production orders with exceptionally fast turn-around times. From conception to prototyping, to final production runs, our technical representatives and design engineers will work closely with your staff to meet your critical tolerances and specifications. You are guaranteed to receive experienced, professional, and personalized service from the first contact through your on-time delivery, with complete confidentiality and dedication to protecting your good name.